Aluminum Casting Process
To understand what the aluminum casting process is we must first look at the properties of aluminum. Aluminum is the most abundant metallic element in the earth's crust, of which it forms nearly 8%. It always occurs as a compound, some of its minerals being bauxite, cryolite, corundum, alunite, diaspore, turquoise, spinel, and such silicates as kaolin, feldspar, and mica. Bauxite a ferruginous aluminum hydroxide, is the basic raw material from which the metal aluminum is produced.
Impurities are removed from the bauxite by chemical processing to make alumina (aluminum oxide). The bauxite is crushed, mixed in a caustic soda (sodium hydroxide) solution, and then heated by steam under pressure to dissolve the alumina. Settling and filtration remove impurities. After cooling, the solution is agitated and crystals of hydrated alumina are formed. These crystals are washed and then dried in long rotating kilns. The final product, alumina or aluminum oxide is a very hard crystalline substance having the appearance of refined sugar. Four pounds of bauxite yields approximately two pounds of alumina.
Electrolyzing a solution of alumina in molten fluorides makes aluminum; this electrolysis takes place in reduction pots or cells at a reduction plant. Aluminum reduction plants produce pure, high quality primary aluminum. The reduction process removes the oxygen from the alumina, which consists of almost equal parts of aluminum and oxygen, and leaves pure aluminum. Two pounds of alumina yields one pound of aluminum.
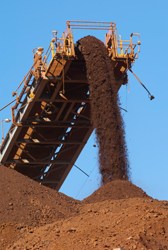
Aluminum is lightweight, has excellent strength, high thermal and electrical conductivity, high reflectivity, good corrosion resistance, excellent workability, and attractive appearance. It can be given almost any finish. It is nonmagnetic, nontoxic, and non- sparking.
Aluminum weighs 1.175 lb/in3, approximately 1/3 the density of steel, copper, and brass. Some of the stronger aluminum alloys exceed the strength of mild steel. The melting point of aluminum is 1215 degrees Fahrenheit.
The high thermal conductivity of aluminum is a marked advantage in any application where it is desirable to conduct or dissipate heat quickly and uniformly. On a weight basis, aluminum is the most efficient heat conductor of the common metals.
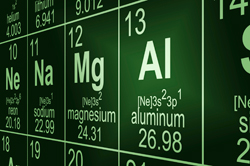
ALUMINUM ALLOYS
An alloy is a substance having metallic properties, composed of two or more chemical elements of which at least one is a metal.
The 6000 series principal alloying constituent is Magnesium silicide. This series has good formability and corrosion resistance, with medium strength. These alloys are the most popular aluminum extrusion alloy class. They have good strength, corrosion resistance, machinabilty, weldability, formability, and are heat treatable. 6063, 6005 and 6061 are produced in Bonnell Aluminum's Carthage, Tennessee and Newnan, Georgia casting facilities. 6463 is only manufactured in Newnan.
- 6063 is the most popular of the aluminum extrusion alloys. This alloy makes a good surface finish, is corrosion resistant, and can be heat-treated for strength. This alloy is used in fabricated parts such as: storm windows, storm doors, storefronts, and commercial buildings. In other words, it is primarily used in nonstructural applications, but occasionally it is used in structural applications.
- 6005 is used in structural applications where more strength is needed. 6005 alloy is also less corrosion resistant compared to the other alloys in the 6000 series. An example of a product manufactured with this alloy is bicycle rims.
- 6061 has good corrosion resistance and is used in transportation and structural applications. This alloy has the highest content of magnesium and silicon of all the alloys in the 6000 series. Examples of products that are manufactured from this alloy are car parts, electrical housings, and material handling systems (i.e. load bearing applications).
- 6463 is manufactured Bonnell Aluminum's Newnan, Georgia casting facility. This alloy is used for making bright extrusions. Bright dip is a very shiny finish created by anodizing the extruded aluminum. Anodizing is a finishing process which puts a protective oxide coating on the aluminum. This alloy has low iron and high copper content to aid in the brightness of the material. It is mainly used in the production of shower and tub enclosures, running boards, and decorative trim.
- 6060 is an alloy also known as easy squeeze. It is primarily used in the aluminum clad window market for products with thin walls and high tongue ratios. This alloy was created to extrude with 20% less pressure.
CHARGING THE CAST FURNACE
Charging the furnace is the first step in the casting process. The cast house is equipped with the following in order to prepare a charge, which is a mixture of raw materials that are melted down to make an alloy. The equipment is as follows:
ALUMINUM CASTING EQUIPMENT
- Pre-heat oven: used to pre-heat prime (prime is 99.9% pure aluminum) before it is added to the furnace. The heat comes from the recuperator and does not require the use of additional gas. Pre-heating is done to remove water from the prime. The presence of water when the metal is placed in the furnace will cause an explosion as the water rapidly vaporizes.
- Recuperator: Hot air from furnace flows over a series of tubes where the air is heated which in turn feeds the burners for the furnace and in turn reduces gas consumption.
- Front-end Loader/ Fork Truck: the front-end loader is a lift with a large bucket that is used to add scrap to the furnace when preparing a charge. The fork truck is used to add prime ingot into the side doors of the furnaces as well as remove dross and stir the mix.
- Furnaces: used to melt down aluminum and cast logs. The furnaces are open well reverb. Open well means there is a well opening in the front of the furnace where is scrap added. The definition of reverb is when the flame does not melt the aluminum but the heat from the walls and ceiling of the furnace. The following diagram will illustrate the above definitions.
The furnaces are powered by natural gas 95-98% of the time. When there is a gas curtailment, propane gas is used. The furnaces are made and lined with 18"- 24" refractory, which is a heat resistant material that comes in two forms: brick and a castable mix.
ALUMINUM CASTING MATERIALS
There are two types of aluminum logs, primary and secondary. Primary consists of pure aluminum and secondary consists of prime and scrap. There are three components used when charging a furnace to make secondary aluminum: prime, scrap, and hardeners. Bonnell Aluminum's Carthage, Tennessee and Newnan, Georgia casting facilities manufacture secondary logs. However, all billets/logs are cast within the Aluminum Association's specifications.
Prime: 99.9% pure aluminum. Prime comes in three forms: T-bars, tub sows, and pig.
- T-Bar and Tub Sows weigh more than fifty pounds
- Pig is prime that weighs less than 50 pounds
- Prime is also categorized by the iron content for example, 10/20 prime tells us there is a maximum of .10% silicon and .20% iron.
Scrap: material purchased from outside sources and that which is generated from within the plant.
Hardeners: Elements, which are added to a bath of aluminum to increase strength and give the final product the characteristics, desired such as finish, strength, and grain refinement. The elements are as follows: Silicon (Si), Iron (Fe), Copper (Cu), Manganese (Mn), Magnesium (Mg), Chromium (Cr), Zinc (Zn), Titanium (Ti), and Boron (Bo). Silicon, iron, copper, manganese, magnesium, chromium, and zinc are used to increase strength and to improve finish. Titanium and Boron are used for grain refinement which is a reduction in the size of the grains, creates a more consistent grain, and better extrudability.
PREPARING THE BATH
The first step in charging the furnace is adding the appropriate amount of alloying agents: scrap, prime, and hardeners. A charge is a mixture of raw materials that are melted down and mixed to make an alloy. Prime and scrap are first added to the furnace. The alloy being cast determines the quantity of scrap and prime to be used to charge the furnace. Prime and scrap are preheated to remove moisture, which would cause an explosion.
ADDING ALUMINUM
To calculate how much prime needs to be added to the furnace you must first know how much of a heal was left in the furnace from the previous drop. A heal is the remaining metal left in the furnace after one heat has been completed. A drop is the act of pulling the pin on the furnace and allowing the aluminum to flow into the pan until the formation of logs is complete. The formula for calculating how many pounds of prime to add is:
Prime (lbs) = [Charge (lbs) - Heal (lbs)] * [Target % of Prime]
Once the prime has melted, scrap is put into the furnace until the furnace is full and allowed to melt. The melting point of aluminum is 1215 degrees Fahrenheit.
DEGASSING/FLUXING
Degassing is the removal of hydrogen from molten metal by bubbling a mixture of gasses up through the melt. Flux is a substance that promotes fusion, especially of metals or minerals. Fluxing causes impurities, such as alkaline, sodium, and lithium, (which cause the material to have a bad finish), to rise to the surface of the bath. Once degassing is complete a sample is taken and analyzed for proper chemical content.
Dross is a mixture of aluminum oxides and non-metallic material, which float to the surface of molten aluminum. Dross is produced whenever aluminum is added to the furnace that has been painted, anodized, or dirty. Dross is skimmed off of the top of the molten aluminum into dross pots. Dross is cooled with argon gas to eliminates the oxygen in the mixture and prevent thermiting. Thermiting is the temperature at which aluminum will burn up. The dross is recycled to recover the aluminum from within it.
ADDING HARDENERS
Samples are taken and analyzed using a spectrometer. A spectrometer determines the concentration of elements in an alloy by comparing the relative intensity of the wavelengths of radiation produced when a sample is struck with an electric spark. Hardening agents, such as silicone and magnesium, are added to bring the concentration of the alloying agents up to the specification of the alloy being cast.
MAKING A CAST
The temperature of the metal must be between 1300-1340 degrees Fahrenheit, the analysis must be within the ranges specified, and degassing must be complete to begin a drop. The casting process used at Bonnell Aluminum is called direct chill casting because the cooling of the log is taking place in the mold itself where water is running through the mold. After all criteria are met the drop can begin. Before tapping the furnace safety equipment must be put on. Tapping is the process of pulling the plug pin out of the furnace so the aluminum can flow into the trough and pan.