blog & educational outreach

Manufacturing Case Study: A-DEC
A leading manufacturer of dental operatory equipment calls on Bonnell to bring aesthetics to their premium dental furniture.
About Our Customer:
For more than 50 years, A-dec has been the world’s leading manufacturer of reliable dental operatory equipment. They continue to work for the betterment of dentistry and embed their values into the work they do every day.
A-dec Provides:
- Dental chairs and delivery systems
- Cabinets and stools
- Dental tools and infection control equipment
A-dec’s Finished Products:
Inspire furniture includes all of the cabinetry and systems that surround the dental chair in the dental operatory.
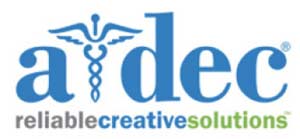
A-dec’s Unique Challenge to Bonnell:
A-dec presented Bonnell with a unique challenge to meet the demand of the growing number of female dentists in the industry.
How could Bonnell help A-dec create a new dental furniture system that delivered A-dec reliability but offered more aesthetic appeal with a focus on appearance and styling improvements?
The requirements
A-dec brought to Bonnell were significant in terms of complexity and scope but were a perfect fit for Bonnell’s custom extrusion capabilities.
The project included:
- 13 shapes making over 100 finished fabricated and/or assembled parts plus 3rd party purchased parts.
- New capabilities in anodized finishing, machining, assembly, racking, packaging, etc.
- A required two-week lead time for parts that have a normal production lead time of eight weeks.
- Very high finish and tolerance expectations.
- Simplifying their products while improving patient treatment productivity.
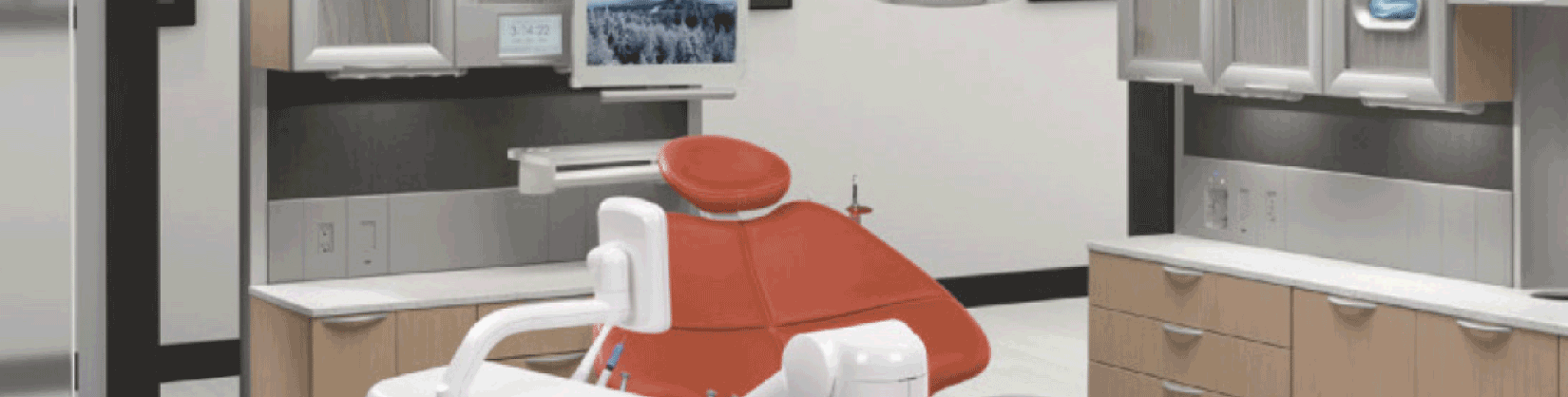
Bonnell’s Key Role:
- Development of new manufacturing capabilities
- Design assistance
- Project Management of A-dec’s Inspire premium dental furniture system.
The Solution:
To meet the unique demands of this project, Bonnell developed a dedicated assembly cell at the A-dec facility and led the continuous improvement process (Kaizen) throughout the initial extruding. Bonnell also implemented a custom replenishment program that prevented production delays previously experienced by A-dec.
Bonnell’s Services to A-dec Included:
- Design assistance
- R&D services
- Extrusion Precision cut Precision CNC machining
- Custom anodized racking to conceal rack marks while anodizing all part surfaces
- Custom anodized finish
- Assembly into finished sub-assemblies
- Custom packing solutions (protective tape and individually packaged)
- JIT stocking program that allows A-dec to offer a 2-week lead time to its customers
- Significant SPC & CPK analysis
The Results:
- A-dec was awarded several prestigious industry awards for their Inspire Dental Furniture.
- Bonnell provided the A-dec Design Engineering Team with technical support and offered extrusion design training onsite while participating in design reviews during product development.
- A-dec entrusted Bonnell with the full value-added process on multiple shapes and on processes where they have strong capability, such as machining and assembly.
FROM OUR CUSTOMER:
“The door frame assembly is “front & center” on this product and requires very high-quality appearance (anodize color must match & die lines have to be minimal!). The 17 assemblies have tight manufacturing tolerances and Bonnell has continued to provide us these assemblies with nearly “seamless” corner connections. Our supply chain team estimated we might see as much as 5% non-conforming on door frame assemblies during production. We’ve actually seen well under .5% during almost 5 years of production.”
Rick Middleton,
Senior Buyer-Dental Furniture Operations
A-dec
ABOUT BONNELL ALUMINUM
Bonnell Aluminum provides a unique mix of high-quality products, along with truly customized solutions and support, to meet our customer’s specific market-driven needs.
Within the competitive marketplaces we serve, only Bonnell Aluminum can offer the unmatched combination of organizational strength, stability and longevity; proven leadership and expertise; breadth and depth of capabilities; and innovative, out-of-the-box solutions to continually meet the highest standards and exceed the expectations of our customers.
With over 1,800 employees and 6 manufacturing facilities located across the United States, our expertise in Lean Manufacturing, Total Productive Maintenance and operational excellence allows us to assign the highest priority to what matters the most to our customers’ business.
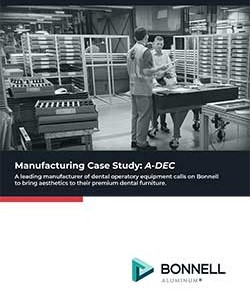