blog & educational outreach

The Advantages of Aluminum Extrusion
A Complete Guide to the Aluminum Extrusion Process and Its Advantages
What is Aluminum Extriusion?
Aluminum extrusion is a fabrication process that forces a heated aluminum billet (a cylindrical log) through a custom-shaped steel die to produce a continuous profile with a consistent cross-section.
This allows manufacturers to create anything from simple angles and tubes to complex architectural systems, all with high dimensional accuracy and excellent strength-to-weight ratios.
How the Aluminum Extrusion Process Works - Step by Step:
Here is a simplified breakdown of the 10-step aluminum extrusion process used by manufacturers like Bonnell Aluminum:
- Die Preparation
A custom steel die is preheated to around 750 to 900˚F. This ensures optimal metal flow and prolongs die life.
- Billet Heating
An aluminum billet is preheated to 800 - 925˚F, making it malleable enough for extrusion without becoming molten.
- Transfer & Lubrication
The billet and ram are lubricated and loaded into the press container to prevent sticking during extrusion.
- Hydraulic Pressing
A powerful hydraulic ram applies pressure—often up to 15,000 tons—pushing the billet through the die.
- Profile Formation
The aluminum emerges in the desired shape, formed precisely by the die's cross-section.
- Quenching
As the profile exits the press, it is rapidly cooled using water or air to control mechanical properties.
- Shearing
Extrusions are cut to manageable lengths at the runout table.
- Cooling to Room Temperature
Cut profiles are cooled fully to stabilize their shape and properties.
- Stretching
Profiles are stretched to correct any twist or deformation; and perform some work-hardening (molecular re-alignment).
- Cutting to Final Length
Final cuts are made - usually between 8 to 24.99 feet—and the profiles may be further aged in ovens to meet specific temper grades (T4, T5, T6).
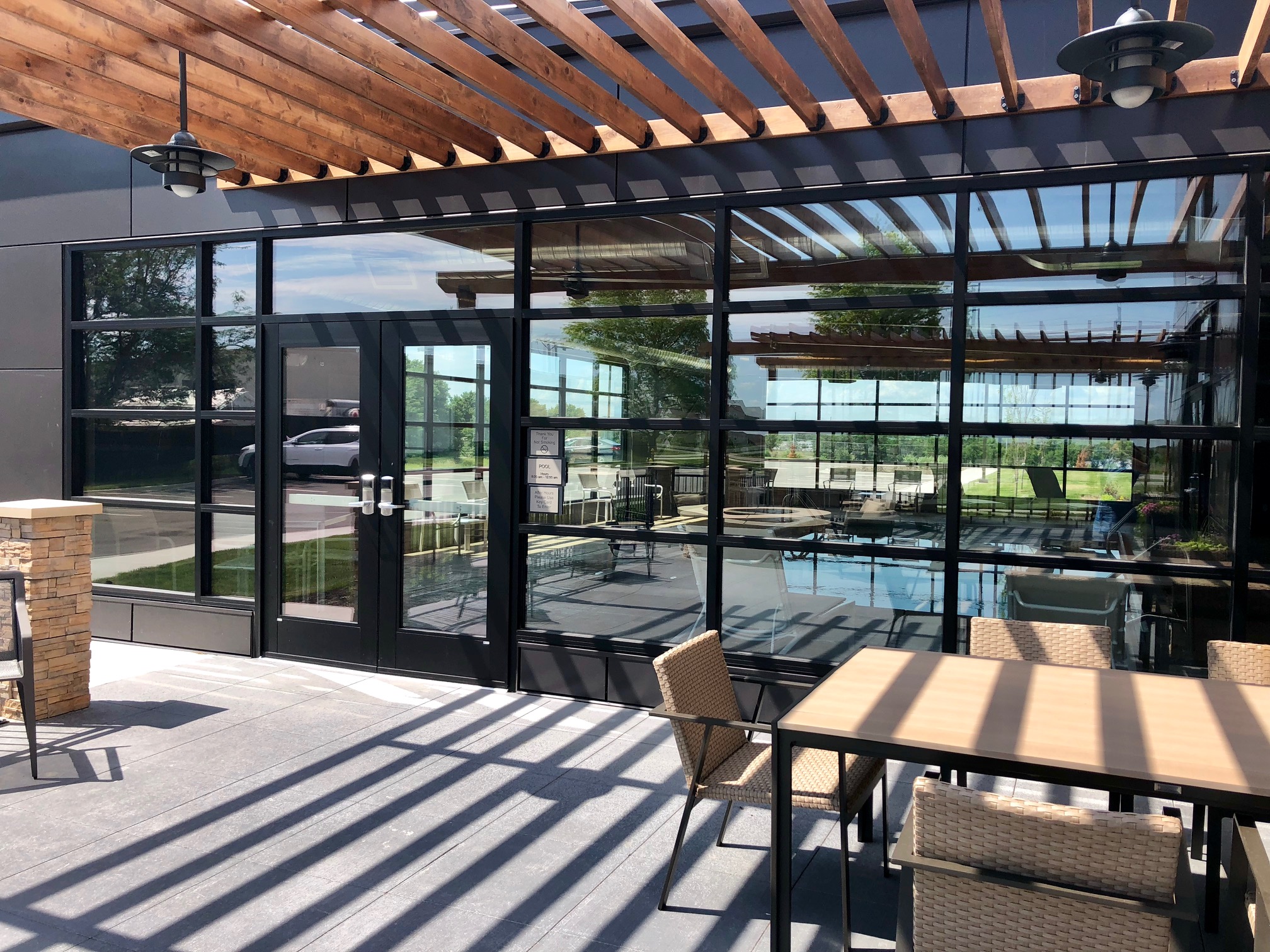
Why Use Aluminum Extrstions?
Aluminum extrusions offer two sets of advantages: material-based and process-based.
Material Advantages
Lightweight – One-third the weight of steel
- High strength-to-weight ratio
- Corrosion-resistant
- Non-toxic and non-combustible
- Thermally and electrically conductive
- 100% recyclable without property loss
Process Advantages
- Near-net shapes reduce material waste and machining.
- Virtually seamless and joinable
- Tight tolerances for complex profiles
- Multiple finishes available – anodizing, powder coating, painting
- Short lead times and lower tooling costs than casting or injection molding
- Ease of fabrication and assembly
A Sustainable Manufacturing Solution
Aluminum extrusion is not just efficient – it’s environmentally responsible.
- Recycled aluminum requires only 5–8% of the energy used to produce primary aluminum.
- Over 75% of all aluminum ever produced is still in use today.
- The process supports closed-loop recycling systems for vehicles, buildings, and consumer goods.
By specifying high-recycled-content extrusions and sourcing from low-carbon smelters, manufacturers can significantly reduce their product lifecycle emissions.
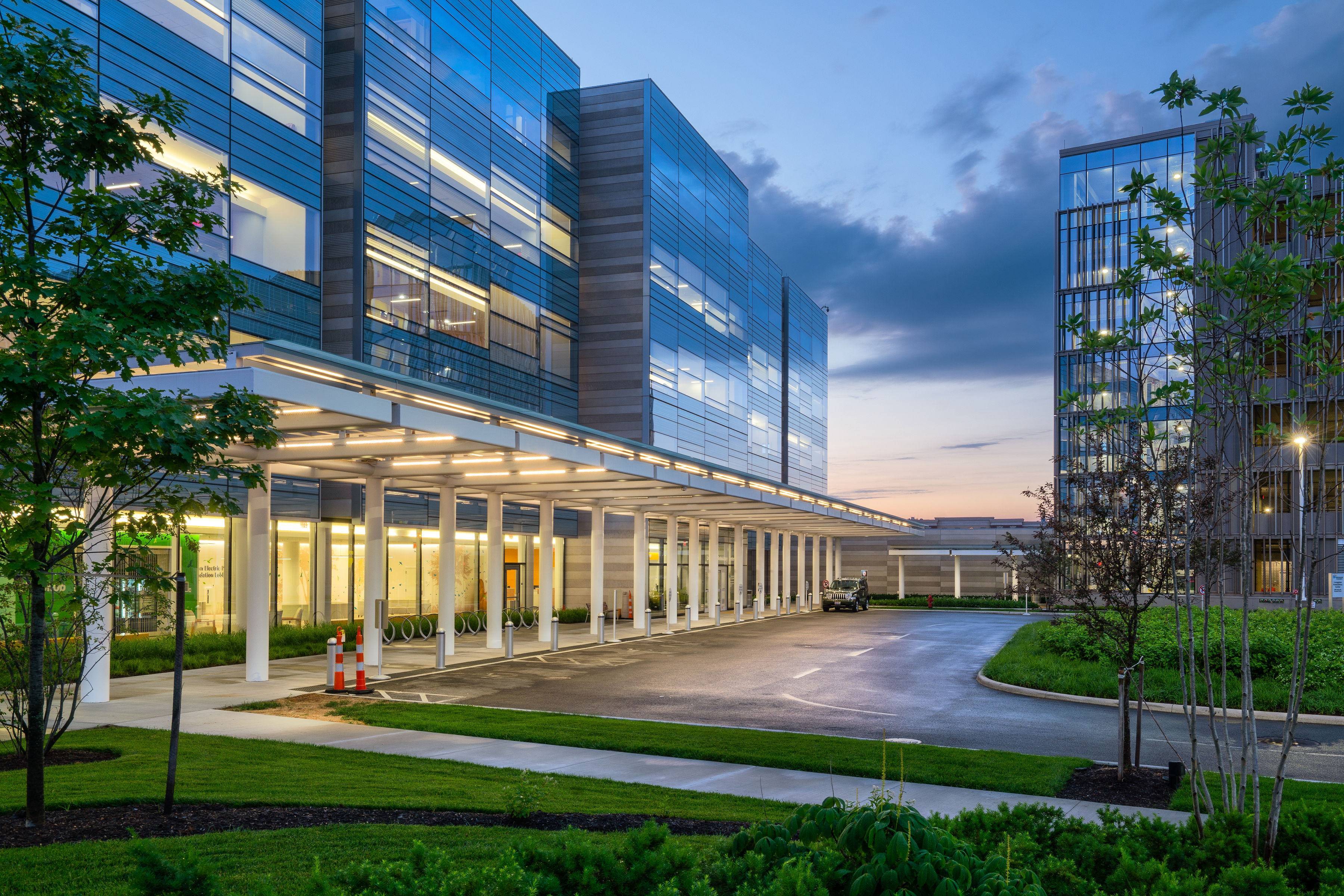
Common Applications for Aluminum Extrusions
- Architecture & Construction: Window frames, curtain walls, sunshades
- Transportation: EV battery housing, Heavy Duty Truck parks (structural), Crash Management systems, Tonneau covers, Roof rails & aftermarket accessories
- Electronics: Heat sinks, enclosures, frames
- Consumer Products: Sporting equipment, furniture, lighting fixtures
- Medical & Aerospace: Patient transfer devices, Medical Workstations, Dental Cabinetry, Telemedicine Kiosk
Choosing the Right Extrusion Partner
For companies looking to leverage the full benefits of aluminum extrusion, it is essential to partner with a provider that offers:
- Custom profile design and die development.
- High-capacity presses and precision tooling
- In-house finishing and fabrication
- Expertise in alloys and tempering
- Commitment to sustainability and recycled content
Final Thoughts: Aluminum Extrusion is Built for Innovation
The aluminum extrusion process offers unmatched value across performance, precision, and sustainability. Whether you are designing next-generation EVs, energy-efficient building systems, or lightweight equipment, extruded aluminum profiles deliver.
Looking to learn more or start your own custom extrusion project? Reach out to Bonnell Aluminum, a qualified extrusion manufacturer to turn your designs into durable, high-performance solutions.
Source: Information adapted from the Aluminum Extrusion Manual, 4.2 Edition, published by the Aluminum Extruders Council (www.aec.org). Used with permission for educational and industry awareness purposes.
ABOUT BONNELL ALUMINUM
Bonnell Aluminum provides a unique mix of high-quality products, along with truly customized solutions and support, to meet our customer’s specific market-driven needs.
Within the competitive marketplaces we serve, only Bonnell Aluminum can offer the unmatched combination of organizational strength, stability and longevity; proven leadership and expertise; breadth and depth of capabilities; and innovative, out-of-the-box solutions to continually meet the highest standards and exceed the expectations of our customers.
With over 1,800 employees and 6 manufacturing facilities located across the United States, our expertise in Lean Manufacturing, Total Productive Maintenance and operational excellence allows us to assign the highest priority to what matters the most to our customers’ business.